PET Bottle blow molding machine KHS Corpoplast / SIG Blomax 16
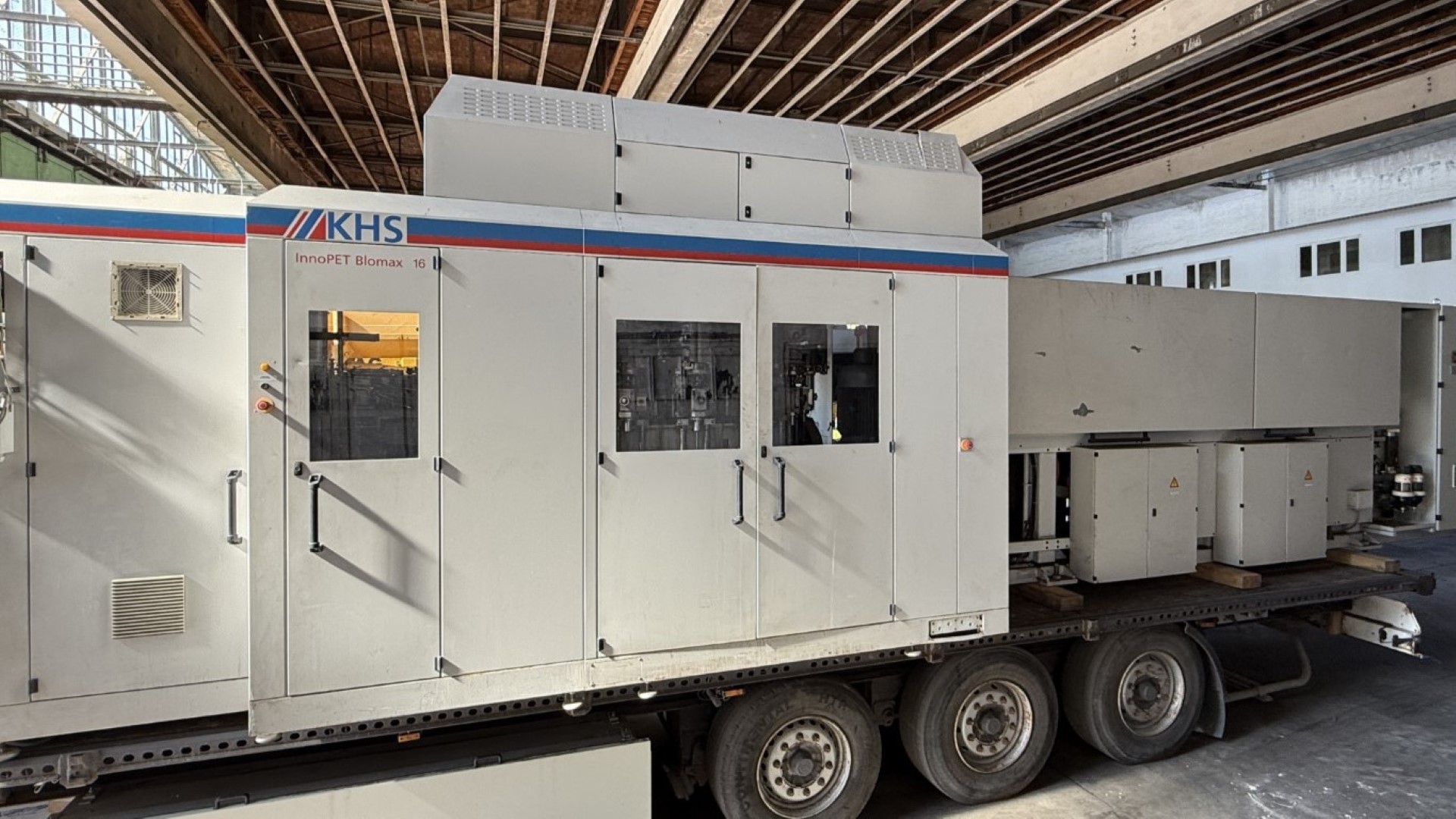
Specifications
Manufacturer | KHS Corpoplast GmbH & Co KG. / SIG |
Model | Blomax 16 |
Year | 2008 |
Condition | Used |
Serial Number | 36-231 |
Stock Number | 1301 |
Type of Machine | PET Blow molding machine |
Capacity | 28.800 bottles/h |
Bottle size | min. 200 ml and max. 2.000 ml |
Bottle neck nominal diameter | 38 mm |
Production hours | 24.288 hours |
Electrics | 380 V - 50 Hz - 3 pH - Earth |
Space requirement | 11,60 x 10,60 x 3,10 meter |
Weight | ± 27.500 kg |
Description
On behalf of our client, we are selling this KHS Blomax 16 PET blow molding machine which is designed for the automated production of PET bottles. It ran together with 2x KHS Absofill / ABF 710 machines before (one of these 2 we are also selling on our website, https://www.hamburg-machinery.com/listings/7469327-used-aseptic-pet-bottle-filling-machine-khs-innosept-absofill-abf-710-03). It is dismantled ± 8 years ago and is stored since in a closed warehouse. The client bought the machine used and decided not to blow bottles themselve, but buy them from another supplier, already blown. This bottle blower is direct available. Loading on the truck / inside the container will be done by the dairy factory.
The machine was used to blow PET bottle for a fruit juice factory in Germany. Capacity: 28.800 bottles/h. Bottle size: min. 200 ml and max. 2.000 ml. Current bottle neck nominal diameter: 38 mm. With the same nominal bottle neck diameter, different bottles shapes and sizes can be blown. Max diameter of the bottle: 115 mm. Length of the bottle: min: 107 mm and max. 350 mm. Length of the prefrom: min. 60 mm and max. 185 mm. Power: 400 V - 3 Ph - 50 Hz - ± 300 kW. Total dimensions: ± 930 x 520 x 310 cm. Space requirement (length x width): 11,60 x 10,60 meter. Weight:± 27.500 kg.
Working principle: The preforms are located in the feed hopper of the inclined conveyor. From here, they are transported to the roller sorter, which aligns the preforms. The preforms are transported via the feed rails to the loading station. Here, they are conveyed to the preform turner. The preform turner takes the preforms individually, turns them, and transfers them to the grippers of the loading station. The loading station places one preform at a time on a transport mandrel of the loading/unloading wheel. From here, the preforms – mounted on transport mandrels – pass through the machine. The preform or the produced bottle remains on the transport mandrel throughout the entire machine cycle. Transfer station I guides the transport mandrels with the preforms placed on them onto the mandrel holders of the linear furnace. Heating boxes with infrared heaters are housed in the linear furnace. At the end of the heating section, a pyrometer approximately 35 mm above the support ring non-contacts the temperature of the preforms. From the heating section, the preforms are transferred from transfer station II to the blow molding stations on the blow molding wheel. The movements of the blow molding station are, opening/closing the blow mold, raising/lowering the base mold, raising/lowering the stretching rod, raising/lowering the blow nozzle are controlled by cams. The "Lock mold" and "Unlock mold" curves are adjustable. The blow molding process consists of the stretching process and a two-stage blow molding process. The first pressure stage (P1) is used to blow the bottle, while the second, higher pressure stage (P2) is used to shape the bottle contour and press the bottle wall against the mold. By utilizing the AR blow air recirculation (AIRBACK®) – which serves to save blow air – the blow molding process proceeds. After the blow molding process is complete, the molds open, and Transfer Station III conveys the transport mandrels containing the finished bottles to the loading/unloading wheel. From here, the bottles enter the bottle turning wheel. Here, they are picked up by grippers, and the transport mandrels are released. From the bottle turning wheel, the bottles are suspended on guide rails and transported out of the machine area by air.
Additional features:
- The touchscreen operation panel is missing.
- Currently no photos available of the feed hopper and the inclined conveyor for the preforms, but these items are included in the quotation.
- Including Riedel cooling system, PC1601S1M496654, year 2008, Refrigerant R407C.